laxu
Rock Star
- Messages
- 7,453
The Kemper Stage should have vent holes in the bottom at least based on product pics. No idea what is under that section, it might be just for some airflow in and exhaust is whatever small gaps there are on the top of the chassis.Not sure where they went wrong in their thinking on the Player. My foot controller (for my KPA Rack) and the KPA Stage don't have holes in the bottom.
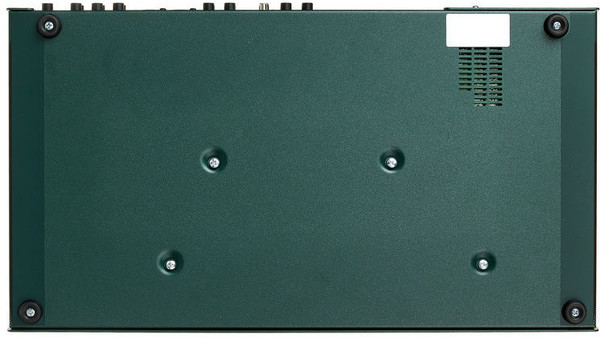
Rain should not be an issue with raised feet like you see above. And if it is, you have way more problems than your gear working.I am guessing that the biggest difference is the size. Maybe they needed the open ventilation because the Player is so small (and therefore has much less surface area for the heat to be transferred out though).
Fractal's FM3 has vents as well (and more of them). Maybe I am the only one that has been rained on at a gig?
Even though the Kemper Player has no feet like that, you aren't really expected to have it plonked on the floor at a gig. Most people would put it on a pedalboard.
For removing heat, you can:
- Use a fan to move air in/out of the chassis.
- Use a heatsink on the hottest components.
- Heatsink + fan.
- Use a metal chassis connected to the hottest components to act as a heatsink. You don't see this often actually because it can still be complicated compared to a basic fin heatsink slapped onto a component.
- Just let air move where it goes as the components can be cooled with only that.